دانلود با لینک مستقیم و پر سرعت .

لینک دانلود و خرید پایین توضیحات
فرمت فایل word و قابل ویرایش و پرینت
تعداد صفحات: 52
نحوه تشکیل
منشأ مواد معدنی
بطور کلی منشأ مواد معدنی را میتوان در موارد زیر خلاصه کرد.
منشأ ماگمایی
ذخایری نظیر کرومیت ، پلاتین ، نیکل ، کبالت و الماس همراه سنگهای اولترامانیکی و ذخایر مس پورفیری و مولیبدن پورفیری همراه سنگهای اسیدی و حد واسط یافت میشوند. بنابراین ترکیب شیمیایی ماگما نوع مواد معدنی را کنترل میکند. نوع ذخایر ماگمایی تابع عمق و مسیری است که ماگما طی میکند. مثلا ماگمایی که از لایه گوشته زمین سرچشمه میگیرد، ذخایر کروم ، نیکل، پلاتین را به همراه داشته باشد و ماگمایی که حاصل پوسته قارهها است قلع ، تنگستن ، اورانیوم ، فلوئور و غیره را همراه خواهدداشت.
منشأ رسوبی
ذخایر گچ ، نمک ، زغال سنگ و آهن لایهای
منشأ دگرگونی
ذخایر کرندوم ، گارنت ، آندالوزیت ، سیلیمانیت و غیره را نام برد.
منشأ گرمایی
ذخایری که در رابطه با محلولهای گرمایی تشکیل میشوند ذخایر سرب ، روی ، مس ، جیوه ، طلا ، نقره و … است. سنگهای مسیر چرخه آب نوع کانسار گرمابی را کنترل میکند سنگهای ولکانیکی اسیدی امکان تشکیل ذخایر نوع طلا ، نقره ، اورانیوم ، سرب ، روی ، … و در سنگهای اولترامافیکی امکان وجود ذخایر گرمابی نوع تیزیت و هونتیت و در سنگهای غنی از سیلیس امکان تشکیل رگههای کوارتز را میتوان داشت.
تاریخچه روی
روی در اغلب کارهای هنری برنزی مربوط به 5000 سال پیش یافت شده و برای مدت 2000 سال به عنوان یکی از اجزاء آلیاژ برنج در اروپا و آسیا مصرف میشده است. چند اثر هنری که سن کانهها به 5000 سال پیش از میلاد مسیح بر میگردد، در اروپا یافت شده است. حدود 200 سال پیش از میلاد مسیح، رومیها که تبحر چشمگیری در ساختن آلیاژهای روی داشتند، از این فلز و آلیاژهای آن سکه میزدند . بنظر میرسد که روی در سال 1000 بعد از میلاد در ناحیه زوار (Zawar) هند ذوب و بر اساس شواهد باستان شناسی در قرن چهاردهم در مقیاس وسیعی تولید میشده است. در طی قرون 17 و 18 شمش روی (Slab Zinc) از آسیا به بازارهای اروپا وارد و با نام روی لحیم کاری یا اسپاتیر (Speiter) فروخته شده است. تکنولوژی ذوب روی در حدود سال 1730 از چین به اروپا برده شد و در سالهای دهه 50-1740 یک کارخانه ذوب روی در انگلیس بر پا شد. تأسیسات عظیم ذوب روی در اوایل قرن نوزدهم شکل گرفت.
در اوایل قرن بیستم با توسعه یافتن تکنیک شناورسازی، بازیابی روی از سنگهای معدنی پیچیده نیز میسر شد و کنسانترههایی با عیار بالا تولید گردید. در قدیم دانشمندان اسلامی روی را قدمیا، قلیمیا و کادمی و ایرانیان آن را«روح توتیا» نامیدهاند. در ایران نیز روی از عهد باستان بکار برده میشده و در بعضی از مفرغهای بدست آمده از آثار باستانی وجود دارد، از قرار معلوم در دوره ساسانیان برنج در ایران ساخته میشده که به آن پرنگ میگفتند. کلمه روی بعد از اسلام ابتدا به مس و سپس به آلیاژ مس و قلع یعنی مفرغ گفته میشد و بعضی اوقات هم قلع را روی مینامیدهاند و گاهی هم نام آلیاژ مس و قلع را اسپید روی گفتهاند.
در سال 1720 در انگلستان ، احتمالا ًبر اساس دانش بدست آمده از روشهای استفاده شده در آسیای شرقی ، برای نخستین بار روی در مقیاس وسیع صنعتی تولید شد و champion جهت تولید روی سازگار با تولید برنج از طریق تصعیر، فرایندی ابداع نمود که بر اساس این فرایند، نخستین فعالیتهای ذوب روی، در 1743 در بریستول، با ظرفیت بیشتر از 200 تن روی در سال بنا نهاده شد .
صنعت روی انگلستان در بریستول و سوان سی (Swansea) متمرکز است . اطلاعات آماری در مورد تولید روی دنیا از سال 1871 موجود است . در این زمان تولید کل برابر 121000 تن در سال بود که 58000 تن آن در آلمان و 45000 تن در بلژیک تولید می شد . تولید کل در آغاز قرن بیستم برابر 472000 تن و در سال 1913 برابر 106 میلیون تن در سال بود .
کاربردهای فلز روی
روی در صنعت ساختمان
روی در ساخت سیمان، دندانسازی، ساخت کبریت، کفسازی، ظروف سفالین، لوازم لاستیکی، اتومبیل سازی، لوازم آشپزخانه، روکش فولاد (گالوانیزه کردن)، تهیه آلیاژهای برنز و برنج، لحیم کاری، قوطی های خمیر دندان، چسب فلز ماشینتحریر، نقره آلمانی و... است.از اکسید و سولفور روی به عنوان ماده رنگی سفید در رنگ سازی و تهیه پلاستیک، از سولفات روی در رنگرزی و ساخت چسب و از کلرور روی در لحیم کاری و جلوگیری از فساد چوب استفاده می شود. پائین بودن نقطه ذوب این فلز که شکلپذیری در ریختهگری را آسان میکند. روی تا اواسط قرن 18 مصرف چندانی نداشت، اما امروزه روی پس از فولاد، آلومینیوم و مس در رده چهارم مصرف قرار دارد. روی در گالوانیزاسیون جهت جلوگیری از خوردگی استفاده زیادی دارد.
یک چهارم روی نیز در ساخت آلیاژهای برنج و برنز و... استفاده میشود. از آندهای روی جهت جلوگیری از خوردگی بدنه کشتیها، سکوهای حفاری و خطوط لوله زیر آب استفاده میشود.
چنانچه روی برای ساخت صفحات روی یا برنج بکار رود، اندازه آلومینیوم آن نباید از 005/0 درصد فراتر رود. مقدار قلع در نوع عیار بالای روی نباید از 001/0 درصد فراتر باشد. مقدار آلومینیم در نوع PW نباید از 05/0 درصد فراتر باشد. فعالیت شدید الکتروشیمیایی، باعث جلوگیری از خوردگی کاتدیک در فرآوردههای آهن و فولادی میشود. آمیختگی روی با مس و تشکیل آلیاژ برنج که این آلیاژ دارای ویژگیهایی مانند قابلیت استفاده در درجه حرارتهای پایین، محافظت در برابر خوردگی و پرداخت زیبا است.
دو عیار دیگر برای فلز روی به منظور مصارف گالوانیزه کردن مورد قبول واقع شده است. یکی به نام عیار گالوانیزه کردن پیوسته (Continuous Galvanizing Grade) که تا 35% سرب و مقداری آلومینیم دارد. و دیگری به نام عیار کنترل شده سرب (Controlled Lead Grade) که کمتر از 18% سرب دارد و بهدور از آلومینیم است.
قالبهای گوناگون (از نظر شکل و اندازه) روی تجاری (Commercial Zinc Cast) را به نام شمش روی (Slab Zinc) مینامند که وزن آن بطور معمول 35 کیلوگرم است ولی ممکن است تا 907 کیلوگرم هم برسد. هر قالب روی را با حک کردن عیار و نام تولید کننده آن مشخص میکنند.
از دیدگاه تاریخی روی پرایک وسترن(Prime Western) نخستین نوع مشخص شده بوده و برای گالوانیزه کردن روش هاتدیپ(hot-dip) مصرف میشده است. از زمانی که قالبریزی دقیق قضاوت پیچیده بوسیله آلیاژهای با درصد آلومینیم کم آغاز شد از روی عیار بالا و سپس از روی عیار بالای مخصوص استفاده شد.
غبار روی(Zinc dust) که در رنگسازی به کار میرود از طریق تقطیر بدست میآید. اندازه ذرات آن را با میزان تقطیر و تغلیظ کنترل میکنند. غبار روی با عیار استاندارد دارای 95 تا 97 درصد فلز و بقیه به صورت اکسید است.
مواردی که محتویات فلزی کمتری دارند برای رنگسازی مناسب نیست ولی برای صنایع شیمیایی مناسب هست. ایجاد ذرات غبار روی استاندارد بین 7 تا 9 میکرومتر است. چنانچه اندازه ذرات آن 5/4 تا 7 میکرومتر باشد آن را بسیار ریز دانه (Super Fine)، و اگر ابعاد ذرات 5/2 تا 5/4 میکرومتر باشد آن را فوق ریزدانه (ultra fine) مینامیم.
پودر روی با اسپری کردن یک جریان مذاب فلزی و با استفاده از جریان فشار قوی هوا یا گازهای دیگر تولید میشود. این ذرات که به گونهای محسوس بزرگتر از ذرات غبار روی حاصل از تقطیر
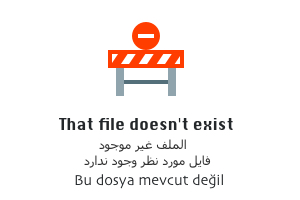